As the giant bucket of scrap metal dumped its load into a furnace of molten steel, an explosion reverberated through the plant. Flames and sparks erupted like lava from a volcano.
That’s what happens when cold, wet metal hits a stew of its liquefied counterpart at 3,127 degrees F.
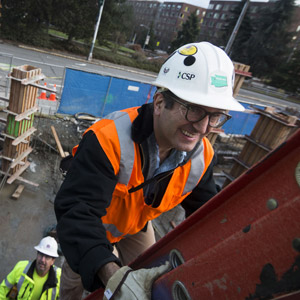
A group of University of Washington School of Public Health graduate students stood transfixed.
“This is the coolest thing I’ve ever seen,” said one student.
“I need to high-five somebody,” said another.
The students – enrolled in a class designed to help them recognize potential health and safety hazards in industries – were shielded safely behind a glass wall at the Nucor Steel plant in West Seattle. They also wore hard hats, safety glasses, and ear plugs.
The group of more than 20 students was touring the plant with their instructors, Marty Cohen and Noah Seixas. The hands-on class offered by the Environmental and Occupational Health Sciences department features visits to industrial sites or workplaces.
Over the fall quarter they also visited a foundry, a lead-acid battery manufacturer, a large cabinet shop, a construction site, and a commercial laundry. Students researched one industry a week, then made a site visit the following week, writing up reports on potential hazards and how to control them.
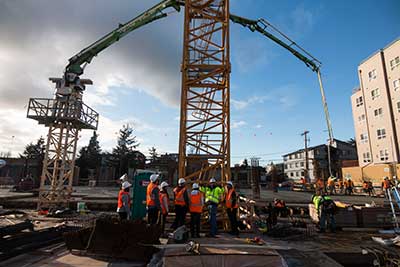
“We want them to learn to be comfortable in an industrial setting, to recognize a variety of hazards and to identify work processes,” said Cohen, senior lecturer and assistant chair of the Department of Environmental and Occupational Health Sciences. “They have to learn to use all their senses properly. But we also want them to base their observations on science, not supposition.”
The class highlights the multi-disciplinary aspects of occupational health and is popular with budding industrial hygienists, doctors in occupational medicine, and industrial engineers.
The visit to Nucor Steel was challenging to evaluate.
“If things are running smoothly, there aren’t many people in harm’s way,” Cohen said. “In addition to typical hazards found in manufacturing, there are some hazards at the facility that have a low probability of occurring but have potentially catastrophic outcomes when something does go wrong.”
Students listed a number of potential hazards, including noise, infrared radiation, heat, burns, and exposure to dust. They queried workers during a guided tour of the plant, which has been producing steel products – mostly rebar –since 1905. That steel has been used to build much of Seattle.

A river of molten metal flowed out of the furnace and into square-shaped tubes where it cooled into long square “billets”. The billets were reheated as they went through rolling mills that eventually shaped them into half-inch rebar.
“We were informed that molten metal emits radiant energy that can lead to eye damage, including cataracts, as well as skin burns,” said Spencer Birch, a graduate student in the department studying exposure science. “Who would have guessed that?”
Birch, who plans to work in manufacturing and intern for Boeing this summer, said the course taught him how to identify workplace hazards while selecting the right engineering and administrative controls. He also learned the appropriate personal protective equipment, such as gloves and respirators, for each type of work environment.
“It was much more than I could have learned from just reading a textbook or going to lectures,” he said. “It’s by far the most informative class I have taken so far in graduate school.”
Esi Nkyekyer, a physician pursuing the department’s Occupational and Environmental Medicine degree, said the course helped her better understand health and safety hazards commonly seen in many industries.
“It provided a framework for better understanding the context within which occupational injuries and diseases occur, and also equipped me to make informed recommendations about how these injuries and diseases can be prevented,” she said. “On a population level, this course brought home the importance of regulations and standards in protecting overall worker safety.”